
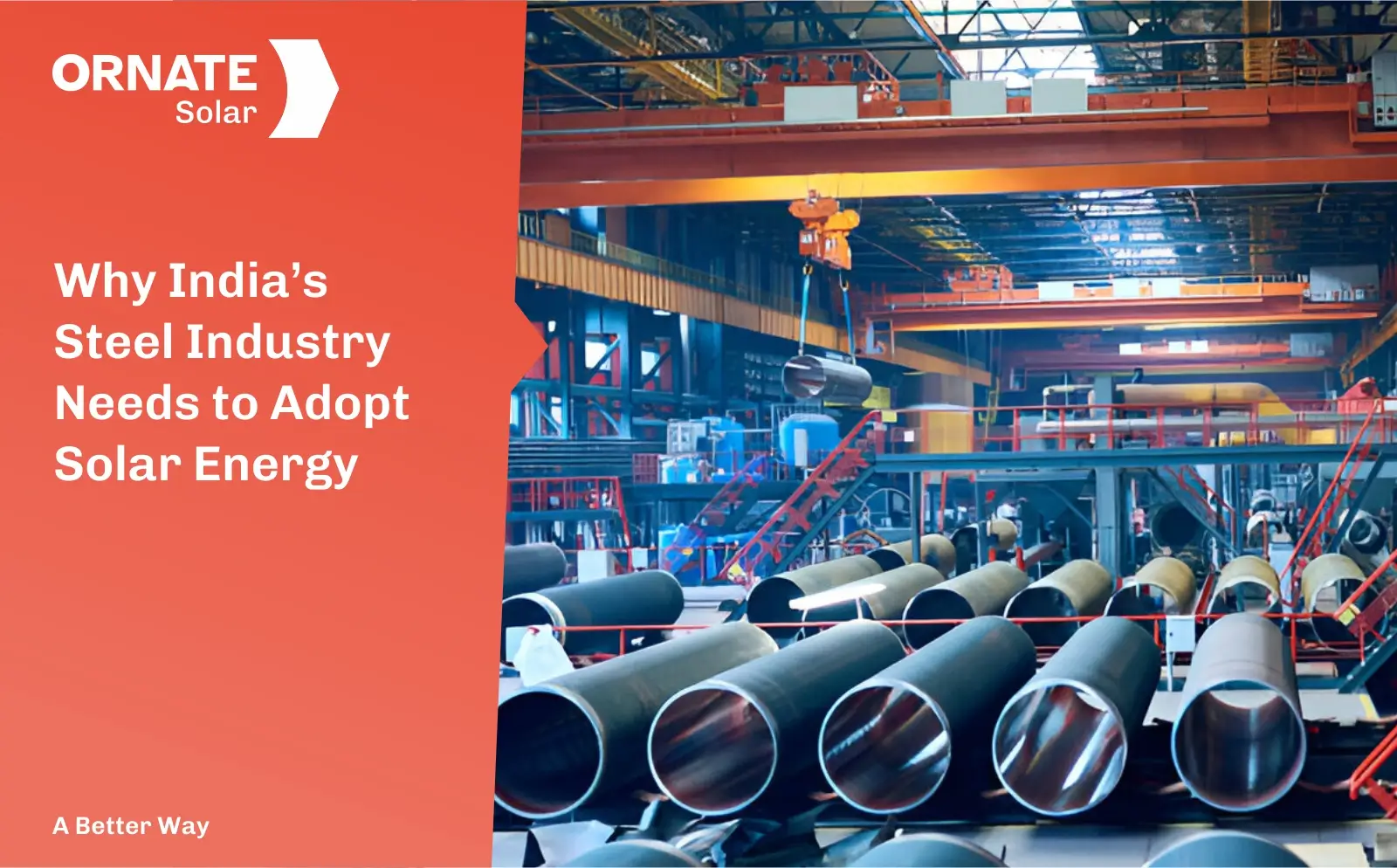
India has the world’s second-largest steel industry and is the third-largest consumer of steel. The steel sector, like that of every other industrializing nation, is critical to India’s economy, generating about 2% of GDP and employing around 2.5 million people in steel and associated industries (MoS 2019).
However, the iron and steel industry also ranks first in terms of CO2 emissions. Let’s understand how the industry can benefit from solar.
Potential
In the steel manufacturing process, the operation of sinter plant, calcining plant, coke oven, blast furnace blowers, basic oxygen furnace, oxygen plant, slab casters, and rolling mills require electricity. However, the primary source of electricity in this giant sector is still coal.
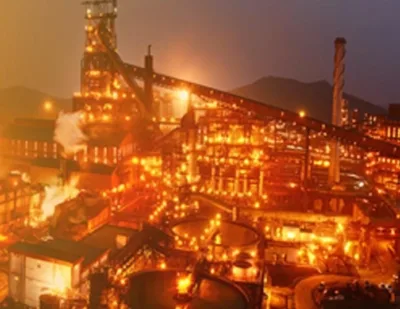
Many iron and steel companies in India have set up captive electricity plants to meet the power demand. Coal, natural gas, and diesel account for 91%, 7%, and 1%, respectively, of this captive generation.
As a result, the industry emits 2.6 gigatonnes of carbon dioxide (Gt CO2) per year, accounting for 7% of global energy system emissions and more than all road freight emissions combined.
The Iron & steel industry in India is covered under the Environment Protection Act (EPA) AND Environment Protection Rules & Regulations that fall under the Ministry of Environment & Forest. This means that the steel plants have to install pollution control equipment and follow certain prescribed Standards/Norms with respect to limiting their air, noise, and water pollution.
In this scenario, solar has immense potential. Since solar energy is a clean, cheap, noiseless, and localized resource it can help a steel company to reduce their electricity expenses and bring down their carbon emissions.
Benefits of Going Solar for Steel Factory
Cost Savings
One of the primary benefits of switching to solar energy is the potential for significant cost savings. Solar power can provide a stable and predictable source of energy, reducing a steel factory’s reliance on fluctuating fossil fuel prices. A company can save up to 80-90% of energy costs by installing solar panels.
Moreover, you can recover the initial investment of solar installation within 4-5 years.
Energy Independence
Solar energy allows the steel factory to generate its electricity on-site, reducing dependence on external energy sources and reducing the impact of energy supply disruptions.
A company can also opt for off-grid or hybrid solar systems and integrate battery backup for continued electricity supply.
Environmental Impact
Solar power is a clean and renewable energy source that produces minimal greenhouse gas emissions and air pollutants compared to traditional fossil fuels. By using solar energy, a steel factory can significantly reduce its carbon footprint and contribute to mitigating climate change.
It can also enhance its ESG rating and develop a positive public image in the market.
Reduced Operating Costs
Solar panels have low maintenance requirements, which results in reduced operating and maintenance costs over the long term. This leads to improved financial stability and predictability for the steel factory.
Long-Term Investment
Solar panels have a long lifespan, often ranging from 25 to 30 years or more. This one-time investment can provide a stable and reliable source of energy for a steel plant for decades.
Government Incentives and Tax Benefits
Many governments offer incentives, grants, and tax benefits (40% accelerated depreciation on your asset) to encourage the adoption of solar energy. These incentives can significantly lower the upfront costs of installing solar panels and accelerate the return on investment.
Energy Consumption:
India 12.5 X 106 Kcal per ton of Salealble Steel |
|
---|---|
Blast Furnace | 54% |
Sintering | 08% |
Coke Ovens | 12% |
Cold Rolling | 05% |
Hot Rolling | 09% |
Steel Making | 09% |
Slabbing & Blooming | 03% |
Common Solar Solutions Available to Steel Factory
- Captive Solar Plant (Roof/Ground Mounted): Steel factories with access to sunlit roofs can install integrated solar roof panels on top. However, a lot of companies opt for ground-mounted solar plants to meet their demand
- Open Access Solar: Companies with a sanctioned load of a minimum of 100kW have the option of buying solar energy directly from the open market. This way, a consumer will only have to pay for the energy consumer without investing capital in installation.
- InRoof solution: Inroof is an innovative solution that turns solar panels into a waterproof solar roof. With this option, companies can turn their roof into mini solar farms.
InRoof Projects
Jindal Steel and Power Limited, Odisha
3.25 MW | 2,00,000 Sq. Ft.
India’s largest 3.25 MW InRoof project now powers Jindal Steel & Power Ltd’s factory in Angul, Odisha. Covering 200,000 sq. ft. and installed at an impressive height of 20 meters (65 ft), this cutting-edge system highlights the innovation of Ornate InRoof technology at the steel giant’s new facility.
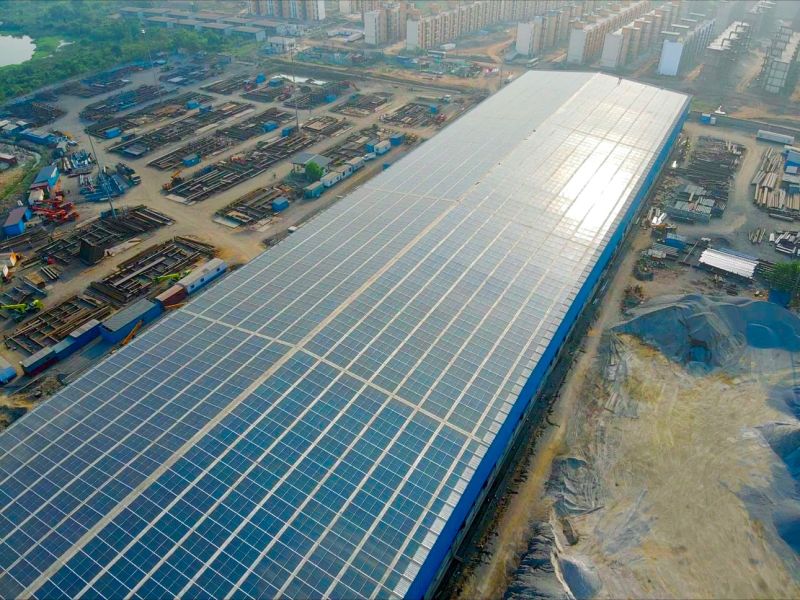
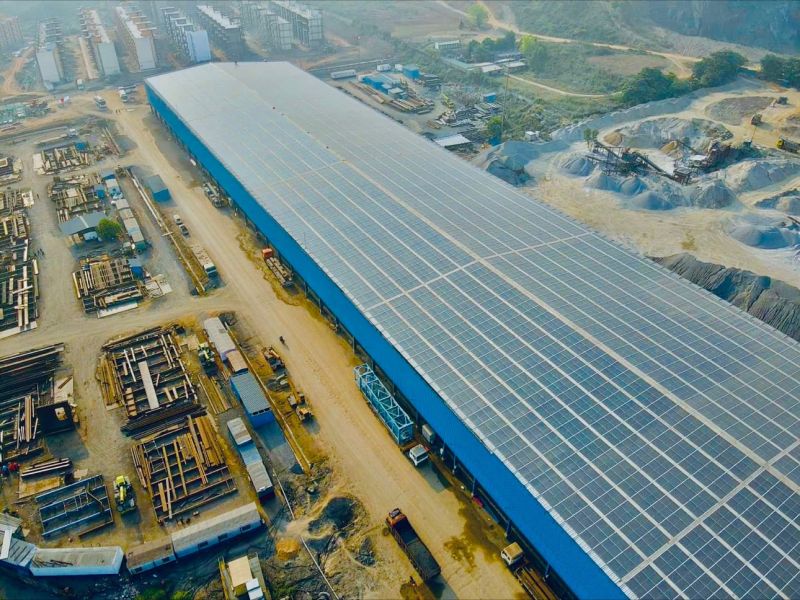
APL Apollo Group, Karnataka
1.45 MW | 87,000 Sq. Ft.
APL Apollo Group, is India’s largest manufacturer of steel pipes and tubes, boasting an annual production capacity of over 2.6 million tons. The organization created the radical rectangular steel tube design and now occupies a 55% share of the steel tube industry in India
The company is setting up a new facility in Malur, Karnataka, and chose Ornate InRoof technology for a clean, cost-effective energy solution. Ornate Solar installed a 1.45 MW system across 87,000 sq. ft., set to generate 2,202 MWh annually and offset over 45,000 tons of CO2 emissions.
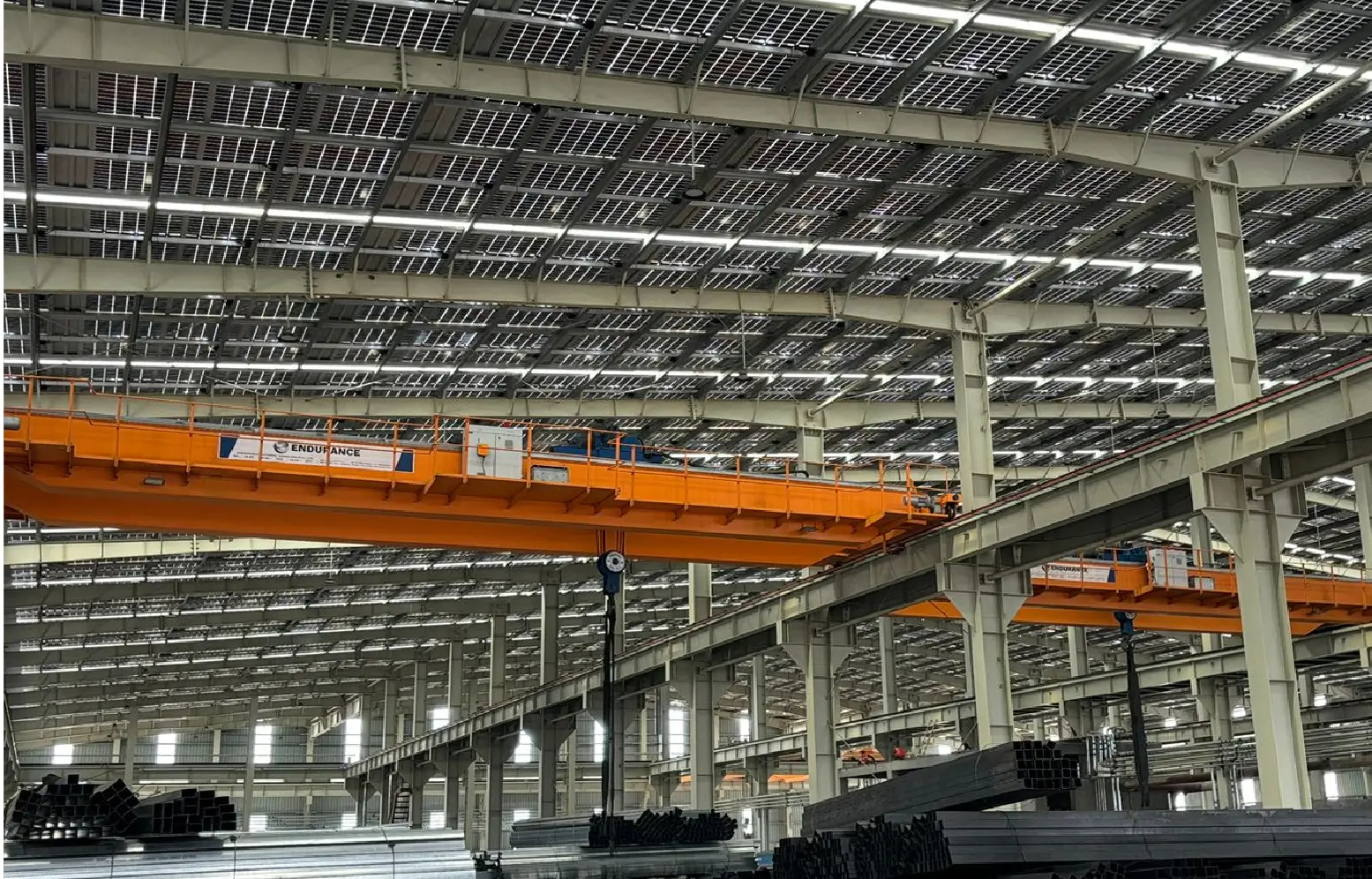
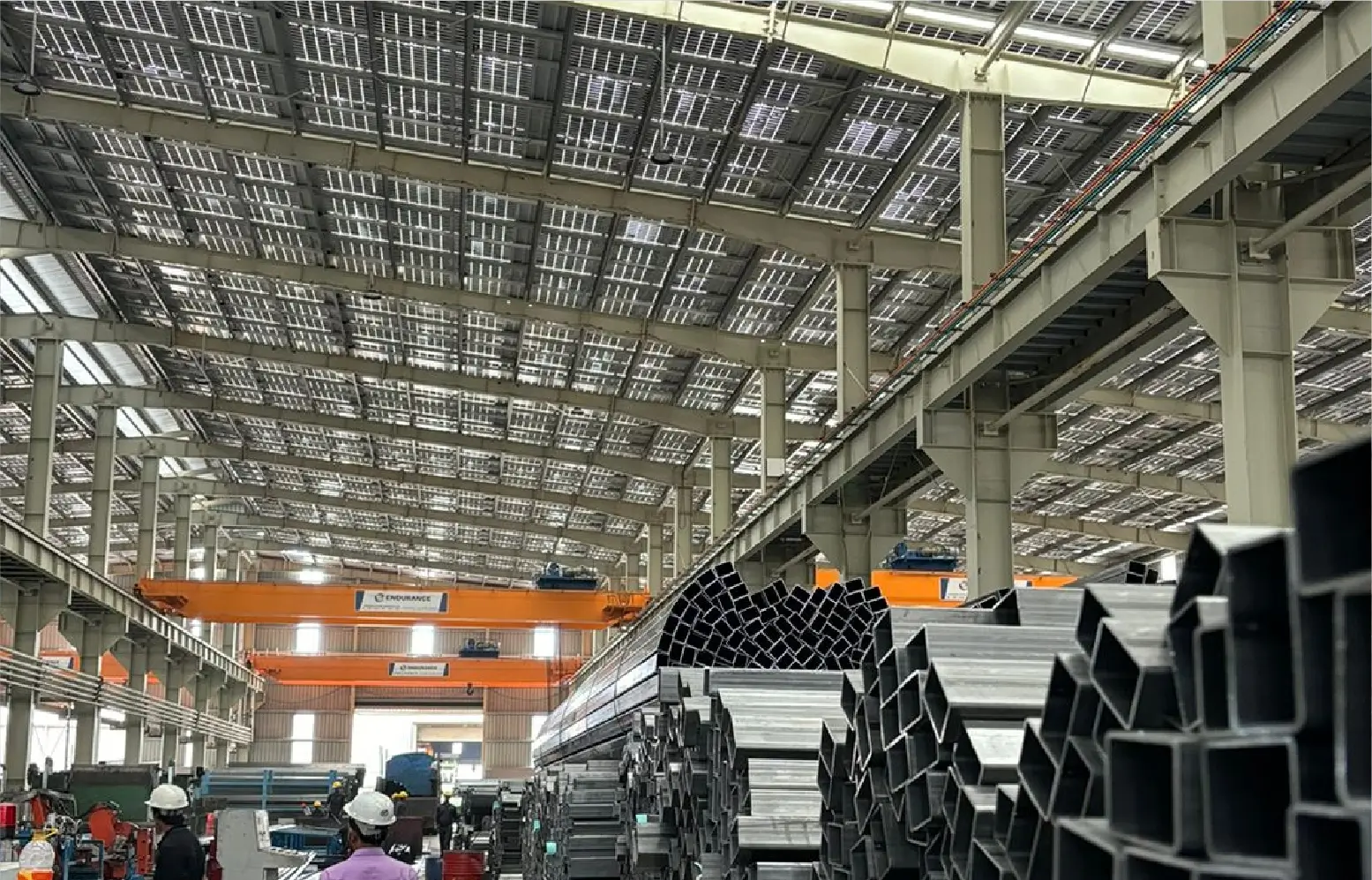
APL Apollo Group, Maharashtra
1.2 MW | 72,000 Sq. Ft.
The company is setting up a new production facility in Maharashtra and wanted to power this building with clean and cost-effective solar energy. APL Apollo opted for the innovation of solar roof to fulfill these conditions.
Ornate Solar has installed a 1.2MW InRoof over a 72,000 sqft roof area for APL Apollo. The InRoof is installed at a height of 14.4m (47ft) and will offset over 30,000 tons of CO2 from the environment.
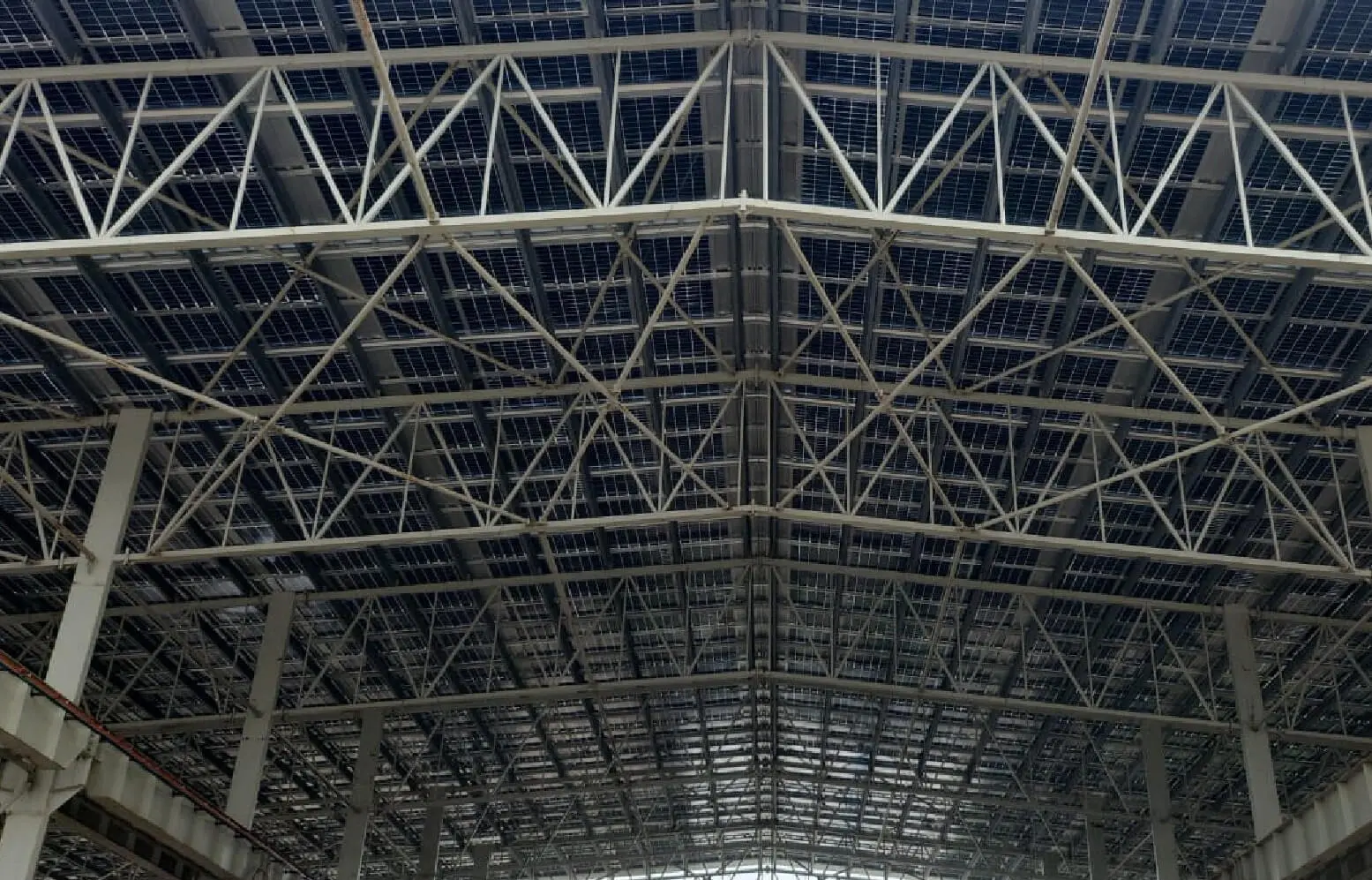
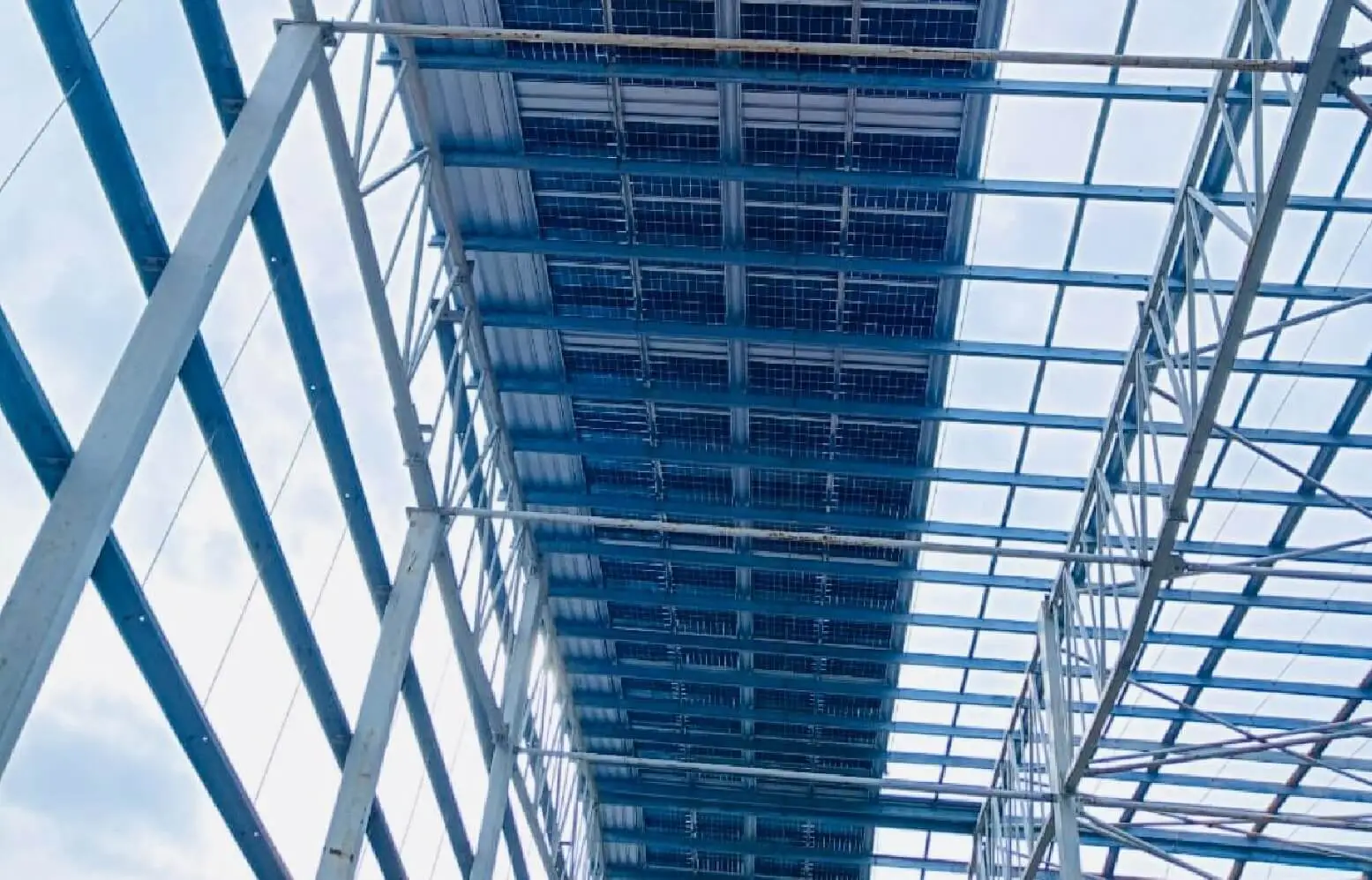
Solar Installations for Steel Industry
Installation Location | Solar Plant Capacity | City |
---|---|---|
Krishna iron strips and tubes PVT LTD | 512 kW | Raipur |
Vikas Stainless Pvt Ltd | 319 kW | Hissar |
Belmarks Metal (India) Private Limited | 79 kW | Indore |
About Ornate Solar?
Ornate Solar is a leading solar company with 10 years of experience in the industry and the mission to reimagine the way solar is installed worldwide.
By not only partnering with the best-in-class solar brands but also manufacturing our high-quality solutions (panels, solar inverters, accessories, InRoof), we develop and deliver solutions that are modern, reliable, and effective.
If you are exploring solar solutions for your steel factory, reach out to us at 1800 2026 252 to discuss your options
Leave A Comment